As a plant engineer or maintenance supervisor, it can feel like walking a tight-rope as you drive improvements in operational and maintenance KPI’s, while having to mitigate risk as you introduce new technologies or methodologies within your operation.
Today, we find that our customers are struggling with this balancing act, particularly with severe service isolation valves. Engineering and maintenance departments have relied upon traditional valve technologies and have instituted rigorous maintenance practices and procedures to ensure that catastrophic valve failures do not occur, thus impacting operations with serious consequences. Even though a plant’s approved valve specification for a particular severe service application may have weaknesses, aggressive maintenance plans can keep valves from failing, but at a high cost in terms of materials and labor costs.
An approved valve specification and maintenance plan is a known entity, and historically a known and established life-cycle cost represented the lowest risk scenario. Industrial markets are now more dynamic than ever, putting an ever increasing pressure on margins. Buyers are becoming more price sensitive and maintenance departments are being asked to deliver improved KPI’s (Key Performance Indicators) with lower annual budgets. It must be acknowledged that even with these financial pressures, changing a valve specification for a severe service application does introduce risk. So how can you optimally mitigate risk while looking to deploy a modern valve technology? We offer three recommendations with examples.
An approved valve specification and maintenance plan is a known entity, and historically a known and established life-cycle cost represented the lowest risk scenario. Industrial markets are now more dynamic than ever, putting an ever increasing pressure on margins. Buyers are becoming more price sensitive and maintenance departments are being asked to deliver improved KPI’s (Key Performance Indicators) with lower annual budgets. It must be acknowledged that even with these financial pressures, changing a valve specification for a severe service application does introduce risk. So how can you optimally mitigate risk while looking to deploy a modern valve technology? We offer three recommendations with examples.
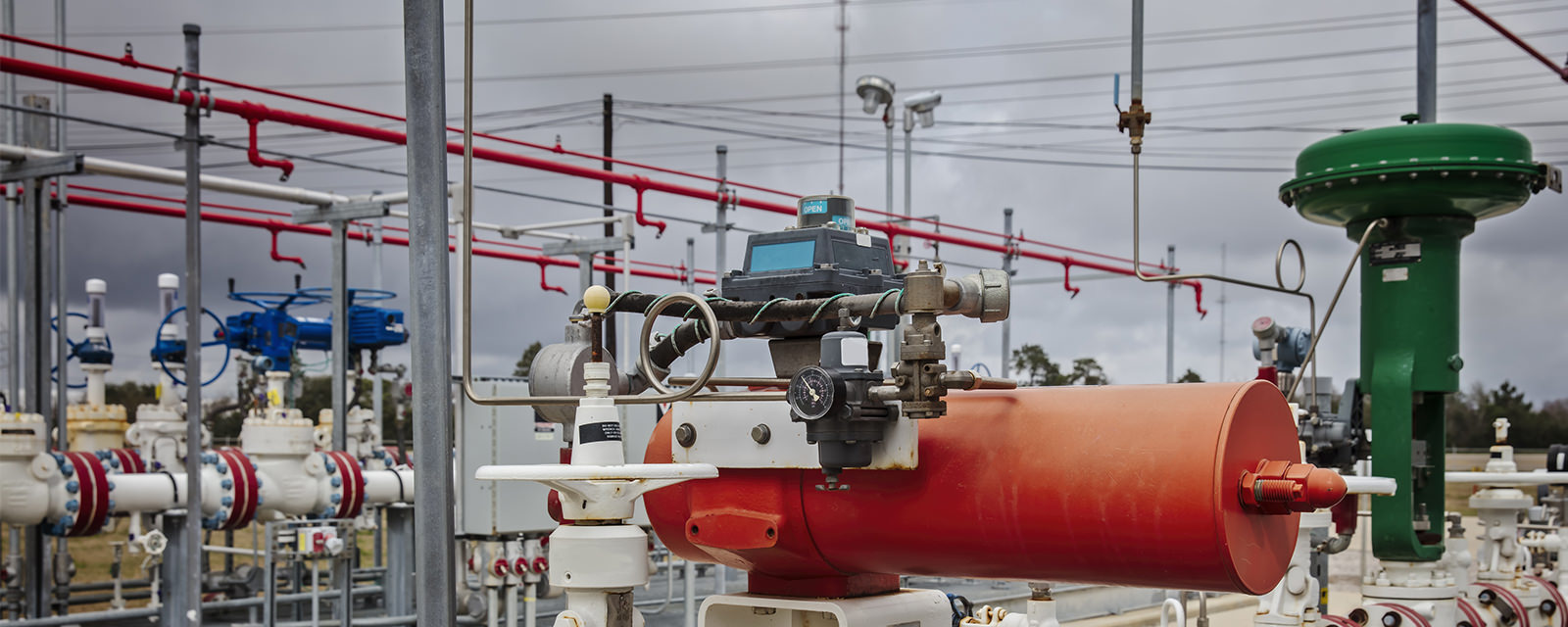
Identify the consistent mechanical failure/degradation of the utilized design and how the modern design, of the proposed valve, eliminates the specific failure mode.
For every valve failure, there is a specific root cause. Generally there are one of two major failure mechanisms involved with severe service isolation valves: the inherent design of the valve is not conducive to the specific application, or the materials of construction within the valve are not compatible with the process media/conditions.
Many severe service applications involving high temperature, high pressure or a process media with particulate require a metal-to-metal sealing mechanism in order to provide a tight seal. The complexity of these designs along with tight dimensional design tolerances, leave little room of variance within the seal design, caused by erosion, impact fatigue or process accumulation within cavities. Maintenance departments can have a good feel for how long they can count on a specific valve to maintain a tight shutoff. Proactive maintenance plans are developed to ensure that a valve’s sealing mechanism is repaired or replaced within the established lifecycle of a valve’s seal. One example of a modern severe service isolation valve design, is a double-eccentric C-Ball design.
Many severe service applications involving high temperature, high pressure or a process media with particulate require a metal-to-metal sealing mechanism in order to provide a tight seal. The complexity of these designs along with tight dimensional design tolerances, leave little room of variance within the seal design, caused by erosion, impact fatigue or process accumulation within cavities. Maintenance departments can have a good feel for how long they can count on a specific valve to maintain a tight shutoff. Proactive maintenance plans are developed to ensure that a valve’s sealing mechanism is repaired or replaced within the established lifecycle of a valve’s seal. One example of a modern severe service isolation valve design, is a double-eccentric C-Ball design.
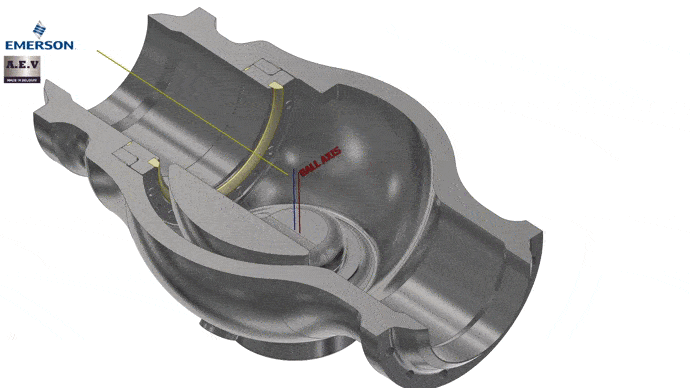
This type of valve does not incorporate a dynamic seating mechanism. A fixed seat is used in conjunction with a cammed eccentric “C” plug that does not come into contact with the seat until the last degrees of rotation. This eliminates potential wear and damage due to impact and impinging.
Choose an initial installation that will allow for periodic performance evaluation and/or inspection.
In order to protect production and safety, the initial installation of a proposed new valve design should allow for periodic evaluations of valve performance and mechanical and material integrity. Modern valve diagnostic equipment can be used to quantitatively monitor the operation and seating profile of the valve. The seating profile of the new valve should be measured before start-up. Subsequent seating profiles will show if there is any degradation of the seating surfaces. Seat profiles are an easy way to validate valve internals, since they are accomplished with the valves in line. Although the process needs to be down and the lines depressurized, the valve does not have to be physically removed.
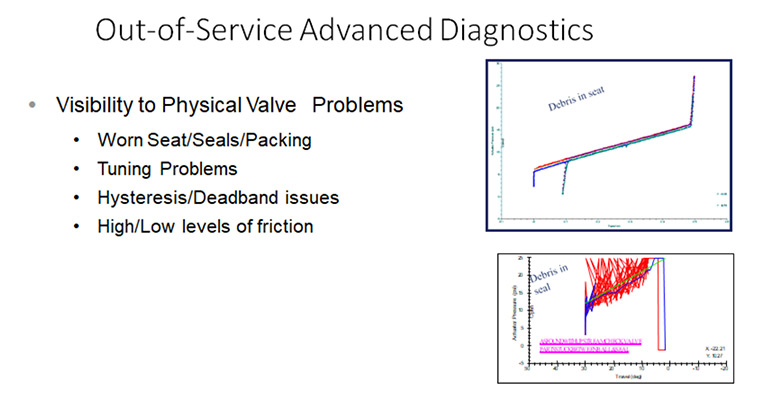
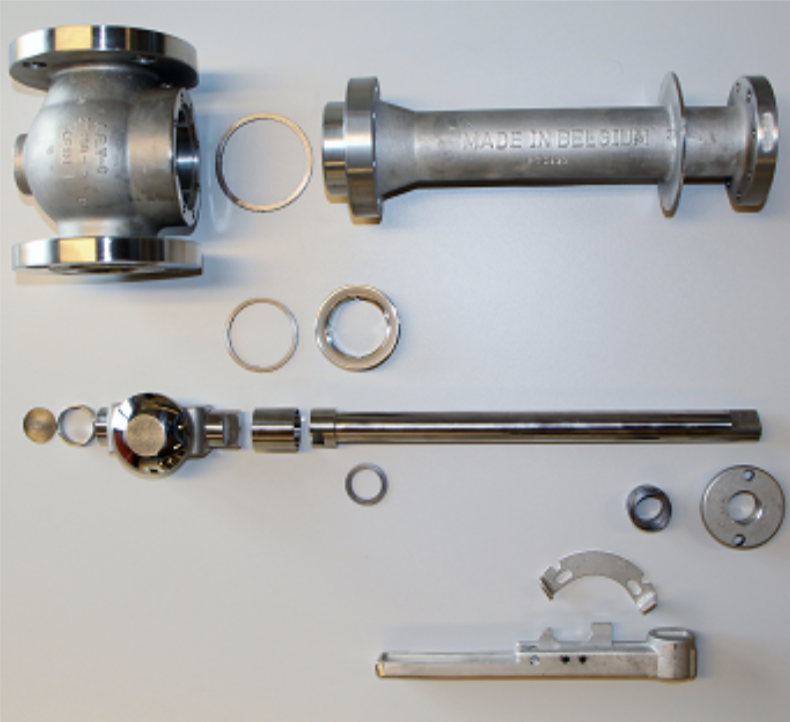
If practical, part of the valve performance evaluation should include removal from the line and a physical inspection of the valve internals. A physical inspection will validate the seating profile and provide definitive feedback on how the new valve is withstanding the process.
Quantify the complete lifecycle cost of the utilized valve design.
Economic rationalization is at the heart of the entire effort to modernize a valve specification for a specific application. The financial components to a ROI is not just limited to the procurement cost of a new valve assembly. The annual spend for valve replacements and parts are a component of the economic equation. The total labor costs for repair and replacement must be factored in, along with financial impact due to lost production. All of these variables add up to a cost of ownership for an existing valve specification. The results of the trial for the proposed modern valve design will allow for the comparison of cost of ownership with the proposed valve design versus current specification.
Learn more
Conclusion
The thought process of updating a severe service isolation valve specification can be daunting due to a perceived risk to the operation, regardless of the extent of the valve’s life cycle cost to the organization. With a rigorous plan to investigate modern valve designs, a formal trial plan with metrics, and with a quantified ROI, risk can be mitigated with an end result of reduced costs and improved operational performance for the organization.Learn more